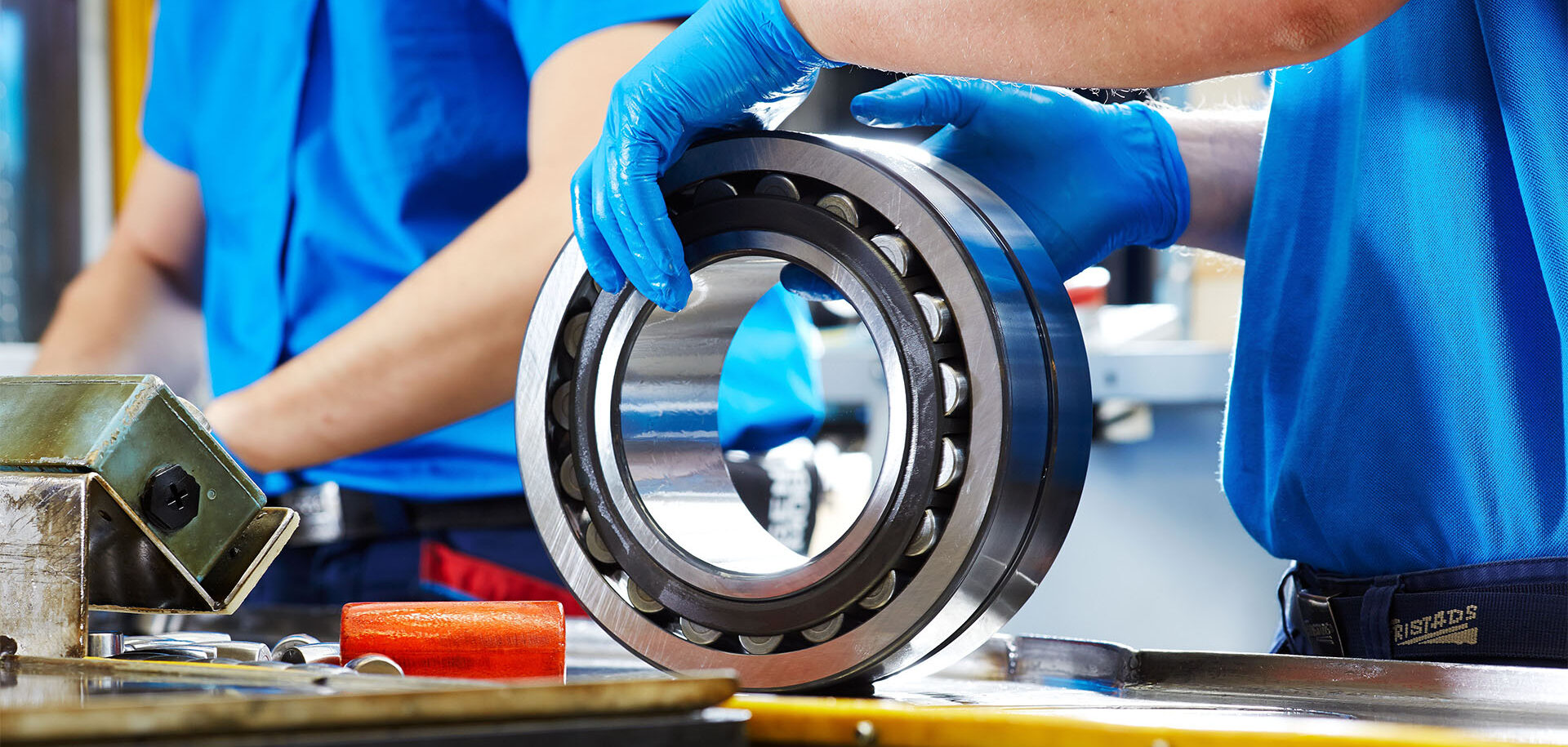
Manufacturing’s lean and digital future at SKF
When Ajay Naik moved from India to Sweden in 2017 to run SKF’s Gothenburg factory, the plant faced multiple challenges. This is how he and his team turned problems into success.
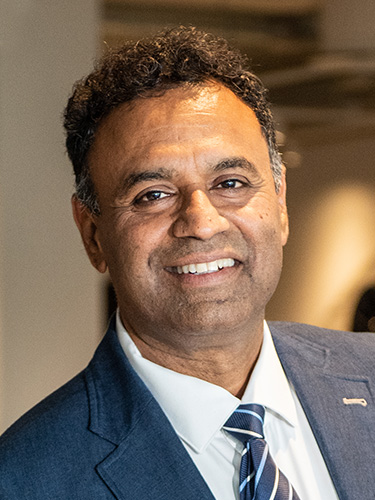
In 2017, at the SKF factory in Gothenburg, an unprecedented surge in global demand arrived just as an overhaul of the factory’s IT systems was in progress. By the summer, orders were piling up and an urgent search for temporary staff was underway to fill acute staffing shortages.
“We just weren’t prepared,” says Ajay Naik, managing director and country manager, SKF Sweden. “We could cope in normal conditions with incremental increases in demand, but the market rose steeply just as we were dealing with internal problems.”
Naik had worked at SKF in India for 30 years and had experience navigating challenges in the manufacturing process. When he came to Sweden in 2017, he used this experience, installing a crisis manager, appointing a supply-chain expert and setting up a crisis room in an attempt to stabilize the situation. By the end of 2017 the worst of the crisis had passed, but a transformative period had begun that would cement the SKF Gothenburg Factory as a global leader in performance. In 2021 the European Organization for Quality recognized Naik with the European Quality Leader (EQL) award for his achievements.
“We just weren’t prepared,” says Ajay Naik, managing director and country manager, SKF Sweden. “We could cope in normal conditions with incremental increases in demand, but the market rose steeply just as we were dealing with internal problems.”
Naik had worked at SKF in India for 30 years and had experience navigating challenges in the manufacturing process. When he came to Sweden in 2017, he used this experience, installing a crisis manager, appointing a supply-chain expert and setting up a crisis room in an attempt to stabilize the situation. By the end of 2017 the worst of the crisis had passed, but a transformative period had begun that would cement the SKF Gothenburg Factory as a global leader in performance. In 2021 the European Organization for Quality recognized Naik with the European Quality Leader (EQL) award for his achievements.
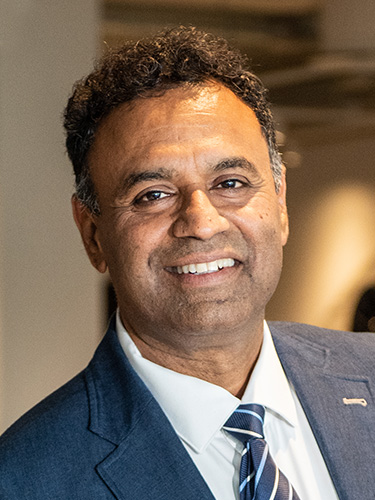
Several measures as a first step of the transformation
The first phase of the transformation began in January 2018 and continued through the summer of 2019 – a period Naik calls the “normalization”. While the IT system was being debugged, the factory introduced a manual supply-chain system. Employee initiatives were introduced to ease stress. Managers increased their presence on the shop floor. Communication improved and a plan to significantly reduce waste was implemented.
We said that we will not paint our walls with colours, we will paint our world with improvements.
Ajay Naik, managing director and country manager, SKF Sweden
“We wanted to become predictable and really reliable,” says Naik. “We also understood that we had huge costs, so we couldn’t be competitive. We could come out of the crisis, but we’d never be profitable with such small margins.”
June 2019 marked the beginning of the performing period. Naik set up workshops to train teams in how to cut unnecessary costs. Management liaised with unions to build flexibility into shift patterns during business cycle upturns and downturns. Where roles were becoming obsolete due to automation, staff were retrained or upskilled.
Working in the Kaizen way
Naik introduced a Kaizen strategy – an approach pioneered in Japan in which employees at all levels work together on incremental improvements to a manufacturing process, and at the factory the best “Kaizer” was chosen each month by unions and employees. Today the walls of SKF Gothenburg are covered in descriptions of more than 5,000 improvements that have been carried out since the strategy was introduced.
“We said that we will not paint our walls with colours, we will paint our world with improvements,” says Naik. “Every wall is like this, so we can see and acknowledge people’s contributions.”
Results begin to show
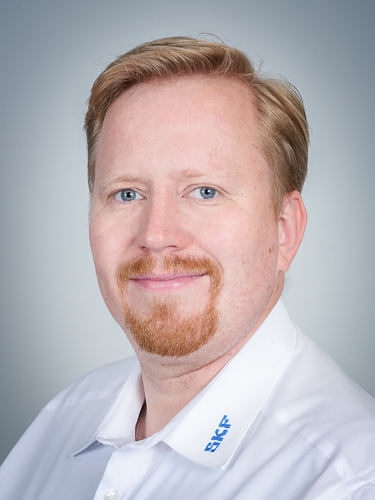
By December 2020, unnecessary costs had been slashed and the plant’s operating margins had improved significantly. When giving Naik the EQL award, the European Organization for Quality said he was selected for his “outstanding accomplishments” in transforming the SKF Gothenburg plant to become one of the top three performing factories in Europe through his “consequent and committed leadership along with a highly committed workforce and team”.
Naik’s success in Gothenburg was all the more remarkable because the SKF factory was among the first to embed a range of new technologies, says Niki Homes, manager of SKF’s Future Factory.
“Naik has made a number of investments in world-class manufacturing channels, along with the challenges of managing new technologies in both data and automation,” Homes says. “The Gothenburg Factory learned to master these new technologies very quickly and is open to developing further, even though the road is at times bumpy.”
Results begin to show
By December 2020, unnecessary costs had been slashed and the plant’s operating margins had improved significantly. When giving Naik the EQL award, the European Organization for Quality said he was selected for his “outstanding accomplishments” in transforming the SKF Gothenburg plant to become one of the top three performing factories in Europe through his “consequent and committed leadership along with a highly committed workforce and team”.
Naik’s success in Gothenburg was all the more remarkable because the SKF factory was among the first to embed a range of new technologies, says Niki Homes, manager of SKF’s Future Factory.
“Naik has a number of investments in world-class manufacturing channels, along with the challenges of managing new technologies in both data and automation,” Homes says. “The Gothenburg Factory learned to master these new technologies very quickly and is open to developing further, even though the road is at times bumpy.”
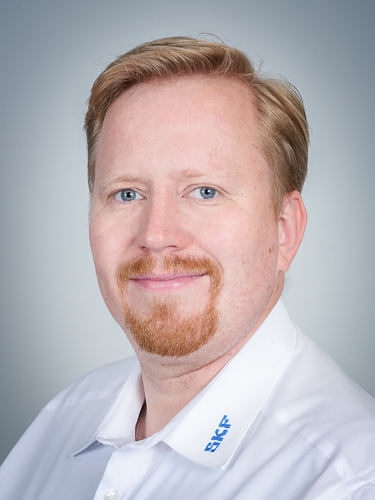
Digital transformation in SKF around the world
Homes is responsible for leading the lean and digital transformation of the nearly 100 SKF factories globally. The changes require embedding many of the new technologies and processes pioneered in Gothenburg and other leading factories around the world, with a view to achieving similar results.
At the core of the digital transformation lies a push to find the right balance between technology, process and people. Only the right balance of all three will enable SKF to unlock the potential power of data to improve its processes, says Homes. That includes raising awareness throughout the company so that all participants are prepared to embrace change, optimizing and standardizing the processes and selecting the right technology to fit SKF’s needs.
“After defining the business needs, the first step has been locating the technology that is most suitable for us,” he says. “Then it’s a question of how we take on board the right technology to support our processes and our people who are executing those processes.”
A key piece of technology that is rapidly improving SKF processes is the hyperconverged infrastructure or HCI. The HCI enables teams to leverage the advantages of both cloud technology and on-site computing power. Calculations needed in real time within the factory can be carried out immediately on the premises, while allowing for more complex tasks to run via the cloud, where more computing power is available on demand.
Ameliorated grinding process
Homes points to precision grinding as an example. A measuring machine calculates the results of the grinding process using an algorithm, he says. It detects the potential for an improvement and gives feedback to the machine to make an adjustment to further improve product quality.
“For many years we have had the ability to measure and react using static algorithms,” he says. “Today, the HCI allow us to continuously feed data from the live manufacturing process into the cloud and continuously and dynamically train our machine-learning algorithms for more accurate adjustments.”
Digitalization is one enabler on the journey to world-class manufacturing. However, says Homes, the lean transformation of SKF’s factories will be the foundation on which the digital transformation is built. His team is guiding and supporting the factories until they are certified when the right conditions are met.
“We need to improve and standardize our processes first,” says Homes. “Then we start with the digitalization. Otherwise, there is a risk that we have digitalized a process still containing waste, which makes solutions more complex and less effective.
Transformation is an ongoing process
“Ajay and his team in Gothenburg executed this structured method – getting all parts of the factory certified in the SKF production system and working closely with all the manufacturing employees to make the transformation happen, all of which supported the great achievements in Gothenburg in recent years.”
For Naik, there is little time to rest while he searches for new improvements to decorate his Kaizen wall of improvements. Preparing his factory for change, particularly from a digital perspective, is an ongoing process that must continue as technology develops, he says.
“We want to build a truly customer-centric organization, so we need to follow our road map – not just to move costs out but also to bring value in,” Naik explains. “That means more focus on sourcing management and the further development of our future competency in the digital journey. It means more change agents and building more on our culture of accountability. This is our journey.”